Mastering Temperature-Sensitive Packaging
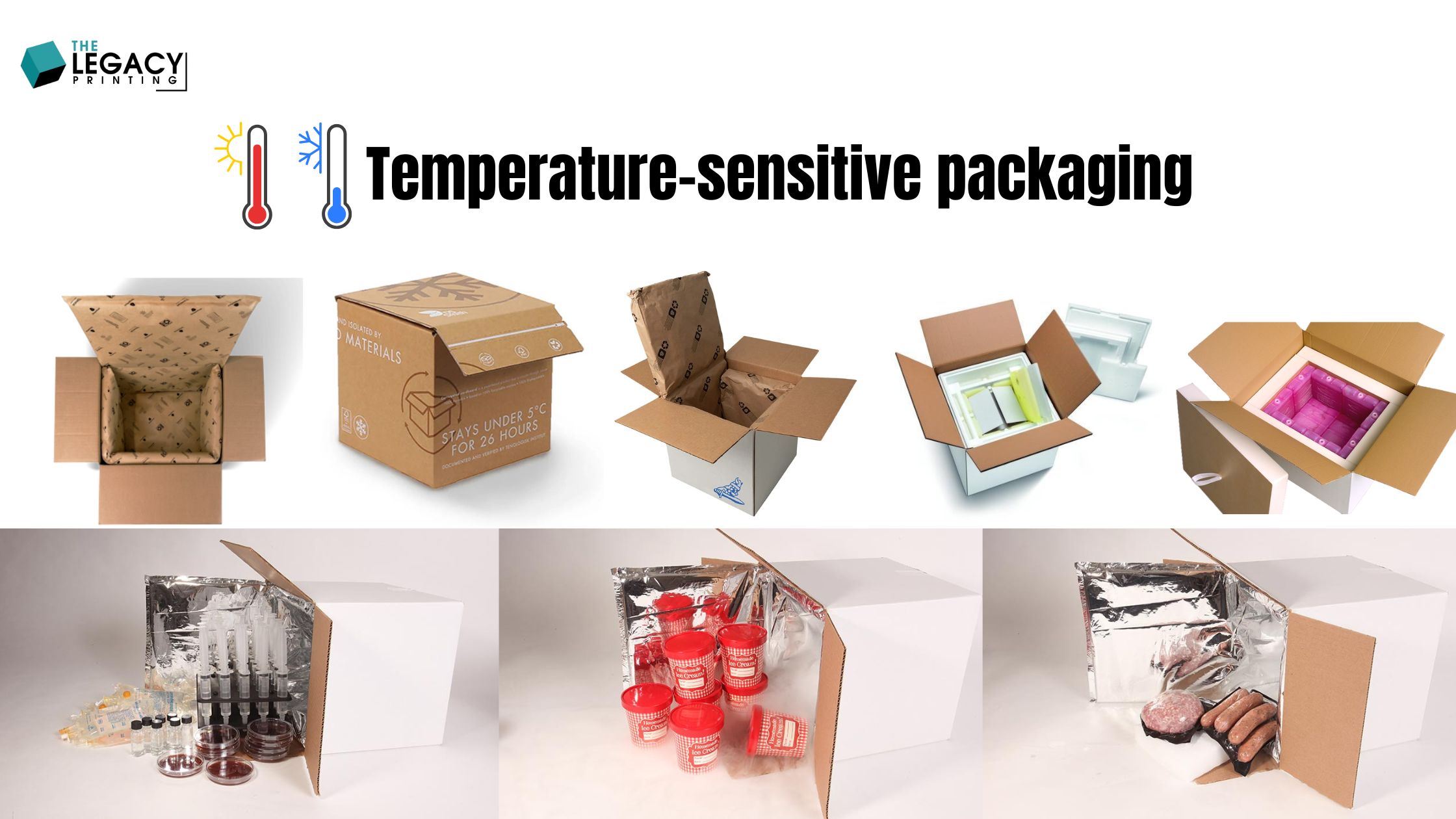
The Vital Role of Temperature-Sensitive Packaging
In a world where global supply chains span continents, delivering perishable and sensitive goods—such as life-saving vaccines, fresh seafood, or cutting-edge biologics—requires precision and reliability. Temperature-sensitive packaging stands at the forefront of this challenge, ensuring that products remain within strict temperature ranges during storage and transit. These advanced systems, combining insulation, cooling mechanisms, and monitoring technologies, are indispensable in industries like pharmaceuticals, food and beverage, and biotechnology. With the global cold chain market projected to reach $447 billion by 2027 (Statista), temperature-sensitive packaging is not just a logistical necessity but a competitive differentiator. This 3,000-word guide explores the science, applications, sustainability, challenges, and future innovations of temperature-sensitive packaging, offering a deep dive into its transformative impact, supported by data, case studies, and in-line references for transparency and depth.
Understanding the Science of Temperature Control
Insulation: The Foundation of Stability
The core of temperature-sensitive packaging lies in its ability to minimize heat transfer, maintaining stable internal conditions despite external fluctuations. Insulation materials like expanded polystyrene (EPS), polyurethane foam, and vacuum-insulated panels (VIPs) are carefully selected for their thermal properties. VIPs, for instance, boast a thermal conductivity of 0.002–0.008 W/m·K, up to 10 times lower than EPS’s 0.03–0.04 W/m·K, making them ideal for ultra-low temperature shipments like mRNA vaccines (Cold Chain Technologies, 2024). By trapping air or creating a vacuum, these materials slow conductive and convective heat exchange, ensuring products like insulin remain within 2°C–8°C during transit across diverse climates.
Cooling Systems: Precision in Action
Maintaining specific temperatures requires sophisticated cooling mechanisms. Phase change materials (PCMs) absorb and release heat at predetermined temperatures, offering precise control for pharmaceuticals, with 55% of shipments using PCMs in 2024 (Pelican BioThermal). Dry ice, effective for ultra-low temperatures like -80°C, is critical for biologics but demands careful handling due to safety risks, including mandatory suffocation warnings per ASTM standards. Gel packs, widely used in food delivery, are cost-effective for short-term shipments, maintaining 0°C–5°C for up to 48 hours. Each cooling system is tailored to the product’s needs, balancing performance with practicality.
Real-Time Monitoring for Assurance
Ensuring temperature compliance requires continuous monitoring. IoT-enabled data loggers, such as those from Sensitech, track fluctuations in real time, alerting logistics teams to excursions that could compromise product quality. In 2024, 80% of pharmaceutical companies adopted smart monitoring to meet WHO guidelines mandating continuous temperature records for vaccines (Packaging Digest). These devices reduce spoilage risks by 20%, providing transparency and ensuring products like chemotherapy drugs remain effective upon delivery.
Real-World Applications Across Industries
Pharmaceuticals: Safeguarding Health
In the pharmaceutical industry, temperature-sensitive packaging is a lifeline for delivering life-saving drugs. Pfizer’s COVID-19 vaccine, requiring storage at -70°C, relies on thermal shippers with dry ice and VIPs, maintaining stability for up to 10 days (Pfizer, 2024). IoT sensors ensure 98% of shipments meet temperature requirements, minimizing spoilage to under 1%. For insulin, local pharmacies use cost-effective EPS boxes with gel packs for last-mile delivery, achieving 90% compliance in 2024 (Packaging Digest). These solutions protect high-value products, ensuring patient safety and regulatory adherence.
Food and Beverage: Delivering Freshness
The rise of e-commerce food delivery has amplified the role of temperature-sensitive packaging. HelloFresh uses wool insulation and gel packs to keep meal kits at 2°C–8°C, reducing shipping costs by 15% and boosting customer satisfaction by 20% in 2024 (HelloFresh). Blue Apron employs compact EPS boxes with PCMs for 48-hour shipments, cutting costs by 10% and increasing subscriber retention by 12% (Packaging World). These systems ensure fresh produce and proteins arrive in pristine condition, meeting consumer expectations for quality.
Biotechnology: Protecting Cutting-Edge Therapies
Biologics and cell therapies, often requiring -20°C to -80°C, demand advanced packaging. Thermo Fisher uses reusable VIP-based containers with PCMs, reducing waste by 25% and shipping costs by 18% in 2024 (Pelican BioThermal). Real-time monitoring ensures compliance with FDA standards, protecting shipments worth millions. This precision is critical for therapies like CAR-T, where even minor temperature deviations can render treatments ineffective.
Table 1: Temperature Requirements by Industry
Industry | Temperature Range | Packaging Solution | Example Products |
---|---|---|---|
Pharmaceuticals | 2°C–8°C, -20°C, -80°C | EPS, VIPs, PCMs, dry ice | Vaccines, insulin, biologics |
Food and Beverage | 0°C–5°C, -18°C | Wool insulation, gel packs, EPS | Meal kits, seafood, frozen foods |
Biotechnology | -20°C to -80°C | VIPs, PCMs, reusable containers | Cell therapies, diagnostic samples |
Source: Cold Chain Technologies and Pelican BioThermal, 2024.
Driving Sustainability in Cold Chain Packaging
Embracing Eco-Friendly Materials
Sustainability is a growing priority, with 70% of consumers favoring eco-friendly packaging (NielsenIQ, 2024). Woolcool uses biodegradable sheep’s wool insulation, which outperforms EPS in thermal efficiency and reduces landfill waste. Recycled PET liners and cornstarch-based foam, adopted by 50% of food delivery services in 2024, offer sustainable alternatives without compromising performance (Packaging World). These materials align with consumer values and regulatory pressures, enhancing brand reputation.
Minimizing Environmental Impact
Optimized packaging design significantly reduces environmental impact. Lightweight VIPs cut shipping weight by 20%, lowering emissions (McKinsey, 2024). Right-sizing, as highlighted by EcoEnclose, reduces material use by 25%, balancing cost and sustainability. Reusable systems, like Pelican BioThermal’s Credo Cube, designed for 100+ uses, cut waste by 30% compared to single-use options (Sustainable Packaging Coalition, 2024).
Advancing Circular Economy Practices
Circular economy initiatives are transforming the industry. PackSavvy offers returnable insulated boxes, reducing waste by 35% for a pharmaceutical distributor in 2024. Compostable PCMs from Phase Change Solutions biodegrade in 90 days, supporting sustainability goals. These practices resonate with consumers, with 65% of Gen Z willing to pay a 10% premium for green packaging (NielsenIQ, 2024), and are particularly strong in Europe, where 75% demand eco-friendly solutions (Euromonitor, 2024).
Navigating Regulatory and Consumer Pressures
Regulatory frameworks are accelerating sustainable adoption. The EU’s 2030 mandate requires all packaging to be recyclable or compostable, with 45% of European companies testing compostable insulation (Euromonitor, 2024). California’s SB 54 mandates 50% recycled content by 2027, pushing brands toward eco-friendly materials. Consumer-driven transparency, like carbon footprint labels piloted by HelloFresh in 2024, aligns with these regulations, enhancing trust and brand loyalty.
Chart 1: Consumer Preference for Sustainable Packaging
Demographic | Preference for Sustainable Packaging (%) | Willing to Pay More (%) |
---|---|---|
Gen Z | 65% | 60% |
Millennials | 60% | 55% |
Gen X | 52% | 48% |
Boomers | 45% | 40% |
Source: NielsenIQ, 2024
Addressing Challenges in Temperature-Sensitive Packaging
Controlling High Costs
Temperature-sensitive packaging is expensive, with insulated boxes costing $5–$50 per unit compared to $0.50–$2.00 for standard packaging (Elements Supply, 2024). Bulk purchasing from Cold Chain Technologies reduces costs by 15%, while reusable systems like Pelican BioThermal’s Credo Cube offset expenses through repeated use. Reduced spoilage rates, 20% lower with smart monitoring (Sensitech), further justify the investment by minimizing product loss.
Optimizing Storage and Logistics
Insulated boxes require significant storage space, posing challenges for warehouses. Collapsible designs from PackSavvy reduce storage needs by 35%, lying flat when not in use. Just-in-time inventory minimizes overstock, while modular warehousing, as implemented by DHL, optimizes space for cold chain logistics, ensuring efficient operations across global supply chains.
Balancing Sustainability and Thermal Performance
Eco-friendly materials must maintain thermal performance to protect sensitive goods. Woolcool’s wool insulation matches EPS in efficiency while being biodegradable, offering a sustainable alternative. Carbon offsetting through partnerships like Carbonfund.org, as practiced by Thermo Fisher in 2024, addresses shipping emissions, enhancing sustainability without compromising quality.
Managing Complex Global Logistics
Global supply chains complicate temperature control, with varying climates and transit times. IoT sensors from Sensitech reduce temperature excursions by 20%, ensuring product integrity. Pre-qualified shippers from Pelican BioThermal streamline compliance across regions, simplifying logistics for international shipments of vaccines or biologics.
Ensuring Regulatory Compliance
Meeting FDA and WHO standards requires meticulous documentation. Automated systems like Avalara streamline compliance by generating accurate temperature records, while pre-qualified shippers with embedded sensors ensure adherence, avoiding fines up to $15,000 per violation (Compliance Gate, 2024). These solutions are critical for pharmaceuticals and biologics, where compliance is non-negotiable.
The Future of Temperature-Sensitive Packaging
Smart Technology for Enhanced Control
The integration of smart technology is reshaping temperature-sensitive packaging. IoT sensors and QR codes enable real-time monitoring and customer engagement, with 40% of cold chain shipments expected to adopt smart systems by 2027 (Retail Dive, 2024). These systems reduce spoilage by 15%, enhancing trust and compliance. QR codes linking to product information, like batch details or usage instructions, add value for consumers, particularly in pharmaceuticals.
Reusable Packaging for Sustainability
Reusable packaging is gaining momentum as brands prioritize circular economy practices. Pelican BioThermal’s Credo Cube, designed for 100+ uses, is projected to cut waste by 30% by 2030 (McKinsey). Incentive programs, such as Blue Apron’s 2024 pilot offering discounts for returned boxes, increased retention by 10%, blending sustainability with customer loyalty. Returnable systems reduce environmental impact while lowering long-term costs.
Next-Generation Materials
Innovative materials are redefining sustainability and performance. Mycelium-based insulation, tested by companies like Phase Change Solutions, uses agricultural waste for a biodegradable alternative, with 50% of companies testing it in 2024 (Packaging World). Bio-based PCMs decompose in 90 days, while lightweight VIPs reduce shipping weight by 20%, cutting emissions. These advancements align with consumer and regulatory demands for eco-friendly solutions.
AI and Automation for Efficiency
Artificial intelligence and automation are streamlining cold chain logistics. AI-driven sizing from PackSavvy optimizes packaging, reducing waste by 25% by predicting ideal dimensions based on product data. Automated packing systems from Ranpak boost efficiency by 40%, enabling high-volume retailers to scale operations seamlessly. Predictive analytics, as used by Amazon in 2024, align production with demand, minimizing overstock and reducing costs.
Transparency and Regulatory Compliance
Consumer demand for transparency is driving innovations like carbon footprint labels, piloted by HelloFresh in 2024, which detail the environmental impact of packaging. The EU’s 2030 mandate for recyclable or compostable packaging is accelerating adoption, with 50% of European companies testing compostable materials (Euromonitor, 2024). In the U.S., California’s SB 54 pushes for 50% recycled content by 2027, encouraging brands to innovate while meeting regulatory standards.
Cost Analysis
Temperature-sensitive packaging is costlier than standard options, with insulated boxes ranging from $5 to $50 per unit compared to $0.50–$2.00 for standard packaging (Shop4Mailers, 2024). However, reduced spoilage rates and enhanced compliance offset costs, with smart monitoring saving 20% on product losses (Sensitech). Reusable systems further lower long-term expenses, making the investment viable for high-value goods.
Table 2: Cost Comparison
Packaging Type | Cost per Unit (USD) | Shipping Cost Impact | Best Use Case |
---|---|---|---|
Standard Packaging | $0.50–$2.00 | Lower (lightweight) | Non-perishable goods |
Temperature-Sensitive Packaging | $5–$50 | Higher (weight, insulation) | Perishable or sensitive goods |
Source: Elements Supply and Cold Chain Technologies, 2024.
Choosing the Right Temperature-Sensitive Packaging
Selecting the optimal temperature-sensitive packaging requires evaluating product requirements, transit duration, and sustainability goals. Pharmaceuticals like vaccines may need VIPs and dry ice for ultra-low temperatures, while food deliveries can use wool insulation and gel packs for cost-effective performance. Testing systems from suppliers like Pelican BioThermal ensures compliance with FDA and WHO standards, balancing cost with performance. Prioritizing eco-friendly materials aligns with consumer preferences, with 65% favoring sustainable options (NielsenIQ, 2024).
FAQs About Temperature-Sensitive Packaging
1. What is temperature-sensitive packaging, and why is it important?
Temperature-sensitive packaging refers to specialized containers and systems designed to maintain specific temperature ranges during the storage and transportation of perishable or sensitive goods, such as vaccines, fresh food, or biologics. These solutions use advanced insulation materials, like vacuum-insulated panels or wool, and cooling mechanisms, such as phase change materials or dry ice, to ensure product integrity. Its importance stems from its ability to prevent spoilage, ensure regulatory compliance, and meet consumer expectations for quality. For example, a 2024 study noted that temperature-sensitive packaging reduced spoilage-related losses by 20% in pharmaceutical logistics (Sensitech).
2. Which industries rely on temperature-sensitive packaging?
Temperature-sensitive packaging is critical across multiple industries. In pharmaceuticals, it protects vaccines and medications like insulin, which require storage between 2°C and 8°C or even -80°C for mRNA vaccines. The food and beverage sector uses it for fresh produce, meal kits, and frozen goods, maintaining temperatures from 0°C to -18°C. Biotechnology relies on it for biologics and cell therapies, often needing ultra-low temperatures. A 2024 report highlighted that 70% of new pharmaceutical products depend on cold chain logistics, underscoring the broad application of these systems (McKinsey).
3. How does temperature-sensitive packaging maintain product temperatures?
Temperature-sensitive packaging maintains product temperatures through a combination of insulation and cooling systems. Insulation materials, such as expanded polystyrene or vacuum-insulated panels, minimize heat transfer by trapping air or creating a vacuum. Cooling mechanisms like gel packs, dry ice, or phase change materials (PCMs) absorb or release heat to stabilize temperatures. For instance, PCMs, used in 55% of pharmaceutical shipments in 2024, maintain precise conditions by changing phase at specific temperatures (Pelican BioThermal). Real-time monitoring with IoT sensors ensures compliance by tracking fluctuations.
4. What are the main challenges in using temperature-sensitive packaging?
The primary challenges include high costs, storage constraints, sustainability concerns, complex logistics, and regulatory compliance. Temperature-sensitive packaging costs $5–$50 per unit, significantly more than standard packaging’s $0.50–$2.00 (Elements Supply, 2024). Storage space for insulated boxes is a hurdle, though collapsible designs reduce needs by 35% (PackSavvy). Balancing eco-friendly materials with thermal performance is tricky, but solutions like biodegradable wool insulation help. Global logistics and compliance with FDA or WHO standards add complexity, addressed by IoT monitoring and pre-qualified shippers (Sensitech).
5. How is sustainability being addressed in temperature-sensitive packaging?
Sustainability is a priority, with brands adopting eco-friendly materials like sheep’s wool insulation from Woolcool, which outperforms traditional foam and biodegrades naturally. Recycled PET liners and compostable PCMs, adopted by 50% of food delivery services in 2024, reduce waste (Packaging World). Reusable systems, like Pelican BioThermal’s Credo Cube, cut waste by 30%, while lightweight materials lower emissions by 20% (McKinsey, 2024). Regulatory mandates, like the EU’s 2030 recyclable packaging rule, further drive sustainable innovation (Euromonitor).
6. What types of cooling mechanisms are used in temperature-sensitive packaging?
Temperature-sensitive packaging employs several cooling mechanisms tailored to specific needs. Gel packs are cost-effective for short-term food shipments, maintaining 0°C–5°C. Dry ice is used for ultra-low temperatures, such as -80°C for biologics, but requires safety warnings. Phase change materials (PCMs) offer precise control by absorbing heat at specific temperatures, used in 55% of pharmaceutical shipments in 2024 (Pelican BioThermal). Compostable PCMs from Phase Change Solutions are emerging as sustainable alternatives, decomposing in 90 days.
7. How do brands ensure regulatory compliance with temperature-sensitive packaging?
Regulatory compliance is ensured through pre-qualified packaging and monitoring systems. The FDA and WHO require continuous temperature records for pharmaceuticals, met by IoT-enabled data loggers from Sensitech that reduce excursions by 20%. Pre-qualified shippers from Pelican BioThermal are designed to meet specific temperature ranges, ensuring adherence. Automated compliance tools like Avalara streamline documentation, helping brands avoid fines up to $15,000 per violation for non-compliance (Compliance Gate, 2024).
8. What are the latest innovations in temperature-sensitive packaging?
Innovations include smart packaging with IoT sensors and QR codes, with 40% of cold chain shipments expected to adopt them by 2027 (Retail Dive, 2024). Reusable systems, like Pelican BioThermal’s Credo Cube, reduce waste by 30% (McKinsey). Bio-based materials, such as mycelium insulation and compostable PCMs, are gaining traction, with 50% of companies testing them in 2024 (Packaging World). AI-driven sizing from PackSavvy cuts waste by 25%, while automated systems from Ranpak boost efficiency by 40%.
9. How does temperature-sensitive packaging differ from standard packaging?
Temperature-sensitive packaging is designed to maintain specific temperature ranges, using insulation like vacuum-insulated panels and cooling systems like PCMs or dry ice, unlike standard packaging, which lacks thermal control. It costs $5–$50 per unit compared to $0.50–$2.00 for standard options (Shop4Mailers, 2024). While standard packaging suits non-perishable goods, temperature-sensitive packaging is essential for perishables, reducing spoilage by 20% and ensuring compliance with strict regulations (Sensitech).
10. How can businesses choose the right temperature-sensitive packaging?
Businesses should evaluate product requirements, transit duration, and sustainability goals. Pharmaceuticals needing -80°C, like biologics, require VIPs and dry ice, while food deliveries at 0°C–5°C can use wool insulation and gel packs. Testing systems from suppliers like Cold Chain Technologies ensures performance and compliance. Eco-friendly materials align with consumer preferences, with 65% favoring sustainable options (NielsenIQ, 2024). Balancing cost, thermal performance, and regulatory needs is key to selecting the right solution.